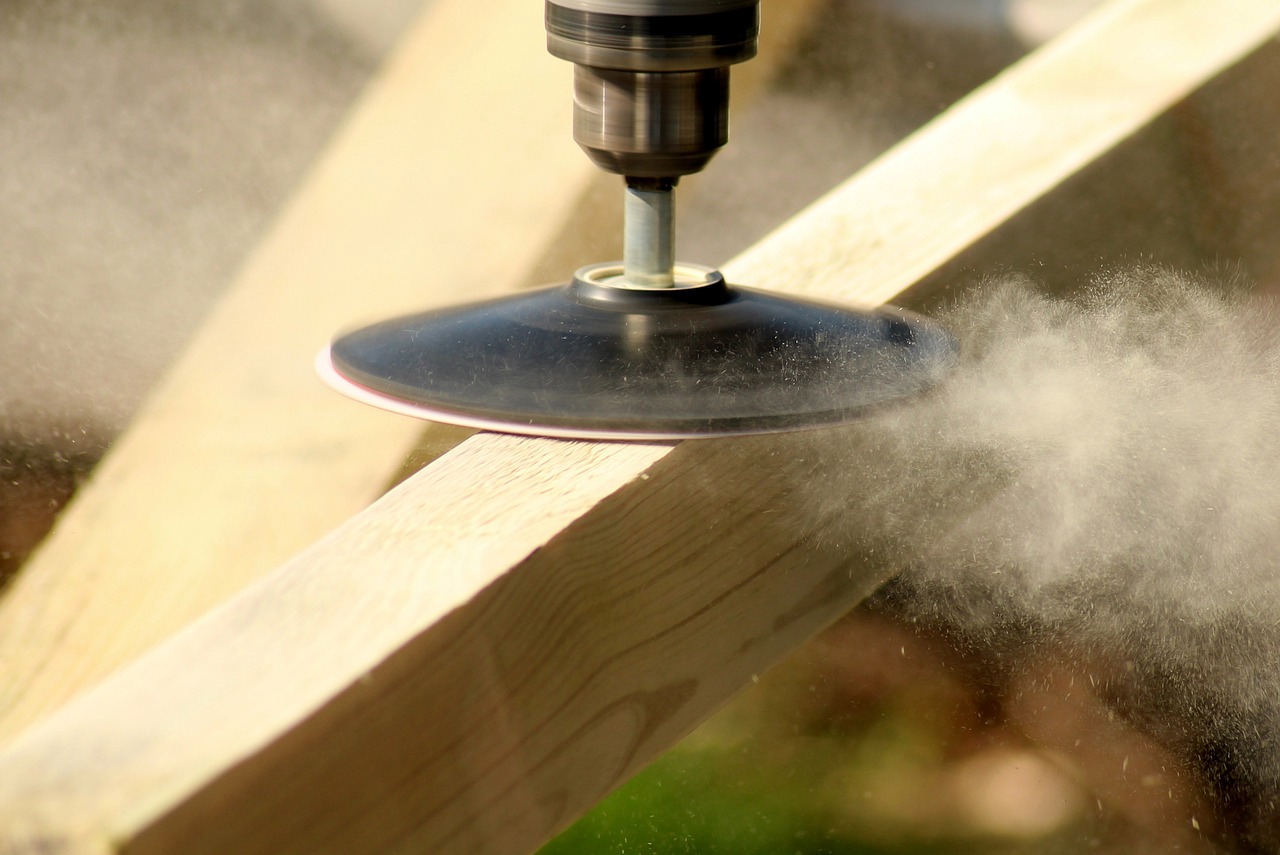
Power tool safety tips
The construction industry is often one of the most dangerous sectors to work in, with accidents including falls from height, slips and trips, and even electrocution amongst the
most common types of non-fatal injuries to occur. While accidents can and will happen, there are some things you can do to limit their occurrence.
PPE
No matter the type of power tools used, the correct Personal Protective Equipment (PPE) should be worn at all times. PPE can include aprons, gloves, goggles, hats, and steel-capped boots. You should ensure that you know which type of PPE or
RPE is required for the job.
If you're working on a construction site, then all staff should be fully trained so they know which is the most effective PPE for the task, and they should be taught how to inspect each piece effectively, as well as the procedures in place for replacing PPE that is no longer fit for purpose.
Using the tools
Regardless of the size or scale of the job, ensuring that you have the correct tools and fittings available for every task is imperative. You should also be able to choose the right attachment that will ensure the job is done correctly and safely.
Once you've chosen the right tool and fitted any attachments, you should make sure it is set to the correct running speed. Setting the speed too fast could not only damage the materials and tools, but could mean that the equipment is unsafe to handle. Too slow, and it won't be productive and could end up damaging the materials.
Tools with mechanical moving parts should also have appropriate safety guards or enclosures to prevent hands, clothing or hair becoming trapped in the moving parts.
Before using the tools, you should understand the full risks associated with them, as well as know the health and safety procedure should something go wrong.
Tool care
Regular inspection and maintenance of
power tools, such as drills, abrasive wheels, and sanders, is the main thing you can do to limit potential accidents and injuries. Not only will this help reduce the risk of injury, but it will it also cut repair costs. By spotting any potential damage you can make a cheaper minor repair, instead of waiting and having to make a larger and more expensive repair at a later stage – which could also impact on production schedules.
Anyone who is using tools should be properly trained, and it shouldn't be assumed that workers know how to use them. On-going training should be carried out at regular intervals to ensure tools are still being used as they should.
All hand-held tools should undergo planned maintenance in accordance with manufacturer guidelines by a qualified person. And notes taken of the outcome of each inspection as well as noting any recommendations.